Products List
- Silica brick for glass kiln...
- BG-98 superior silica bricks for gla...
- Insulating silica brick...
- High thermal shock resistance and ze...
- High bulk density and High thermal c...
- Unshaped refractory Silica Refractor...
- Silica brick for hot blast stove...
- Silica brick for coke oven...
- Silicon brick for carbon furnace...
Classic Case
-
British Refractories customers to
June 7, 2011 the British Refractories Company custo...
-
Turkish customers to visit our fa
On 26 July,2013 Turkey customers visited our fact...
Refractory Knowledge
Refractory Materials Used In the Steel Industry
Date:2017-08-15 10:30 From:Zhengzhou Sunrise Refractory Author:admin
The modern steel production process includes smelting iron ore in a blast furnace into pig iron, injecting molten metal into a BOF or EAF, and then casting molten steel into billets or ingots.
The modern steel production process generally includes material processing, iron making, steel making, rolling, energy supplying and transportation. It is a complex and huge production system.
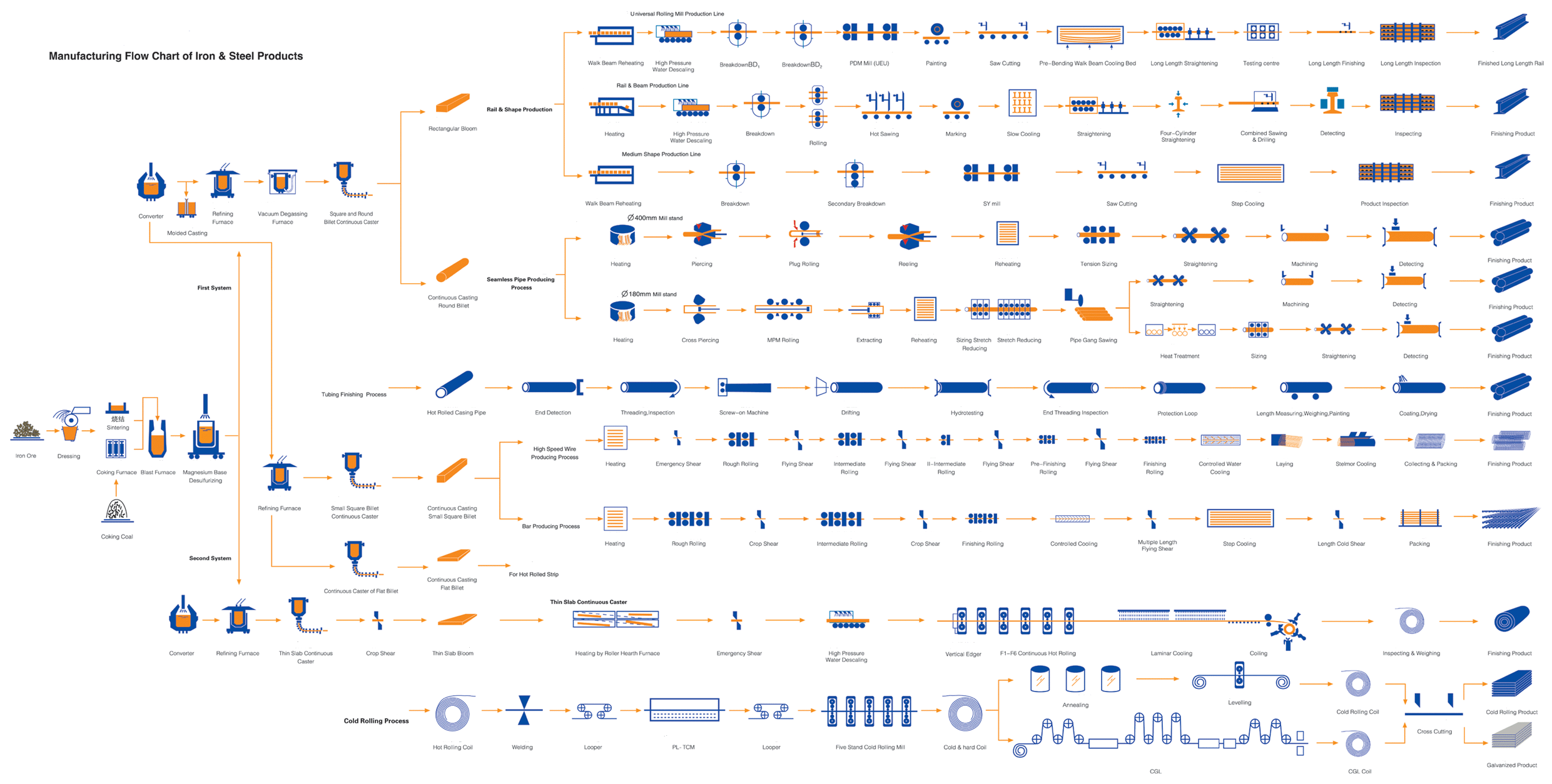
(1) Raw material smelting
Raw materials are the basis of blast Furnace Smelting. Fine materials are the basic guarantee for the stable operation of blast furnaces and high output, high quality, low cost and longevity.
The main raw materials used in the blast furnace include iron ore (natural and artificial high - grade ore), fuel (coke and blowing fuel) and flux (limestone and dolomite). Smelting one ton of pig iron takes about 1.60-1.65 tons of 63% iron ore.
(2) Iron making
Blast furnace iron making is a traditional iron making method fueled with coke. It cooperates with the BOF. It is currently the main method of steel production. The dominant position of the blast furnace for iron making is not expected to change in quite a long time. The nature of the blast furnace iron making is the reduction process of iron. Coke works as fuel and a reducing agent to reduce the iron ore or iron-containing materials from oxides or mineral status (such as Fe2O3, Fe3O4, Fe2SiO4, Fe3O4 • TiO2, etc.) into liquid pig iron.
During the smelting process, charge (ore, flux, coke) is loaded into the furnace from the top through the feeding devices according to the determined proportion. High temperature hot air blown into from the bottom generates reductive coal gas through reaction with coke and liquid slags and forms iron in the hearth by heating, reducing and melting charge. During the rising process, the temperature of the coal gas drops, the composition changes gradually and it finally forms blast furnace gas discharged from the top.
(3) Steel making
Steel and pig iron are mainly iron-based and contain iron-carbon alloy containing a small amount of carbon, silicon, manganese, phosphorus, sulfur and other elements. The difference between them is the content of carbon.
The main steps of steel making includes 1) decarbonization; 2) dephosphorization; 3) desulfurization; 4) deoxy; 5) nitrogen, hydrogen or the like; 6) non-metallic inclusion removal; 7) alloying; 8) heating 9) solidified molding.
The main process of steel making includes: (1) molten iron pretreatment; (2) BOF or EAF steelmaking; (3) refining (secondary refining); (4) continuous casting.
The steel-making process is an oxidation process. The main means of removing impurities is blowing oxygen gas into bath and adding slagging agent to form slags. The decarbonization reaction is the primary means of steel-making process. Silicon, manganese, phosphorus, sulfur and other elements are also removed by the oxidation reaction. The raw materials for steel making include pig iron, steel scrap, flux (limestone), Deoxidizer (ferrosilicon, ferromanganese, aluminum, etc.), alloys and other materials.
(4) Continuous casting
Continuous casting is a step to continuously cast molten steel into billets with a continuous casting machine. Compared to molding, continuous casting has the following advantages:
1) Simplifying the process and energy saving;
2) Reducing the cutting head rate of billets and the metal recovery rate is higher than that of molding by 7-12%;
3) Efficient solidification;
4) Optimized forming.
Continuous Casting process: molten steel is poured into crystallizers through the tundish and rapidly cooled into a solidified shell with a certain thickness, but the inside of the slab is still liquid. The lower portion of the billet connects with a dummy bar extending into the crystallizer bottom. After pouring begins, the casting machine pulls the billets out at a constant speed from the crystallizer through the dummy bar. When billets pass through a continuous casting secondary cooling zone, it is further cooled by water until it is completely solidified. Completely solidified billets are cut into a predetermined length after straightened with a straightening machine and shipped out by the conveyor roller.
(5) Rolling
The rolling process is the process to make workpiece produce plastic deformation by pulling it into the rollers with a different direction of rotation with the friction force between it and the rollers. The general rolling process can be divided into: heating, rough rolling, intermediate rolling, finishing rolling and fine finishing.
During the steel production, since work environments and requirements are different in different furnaces, refractory materials used in them are different.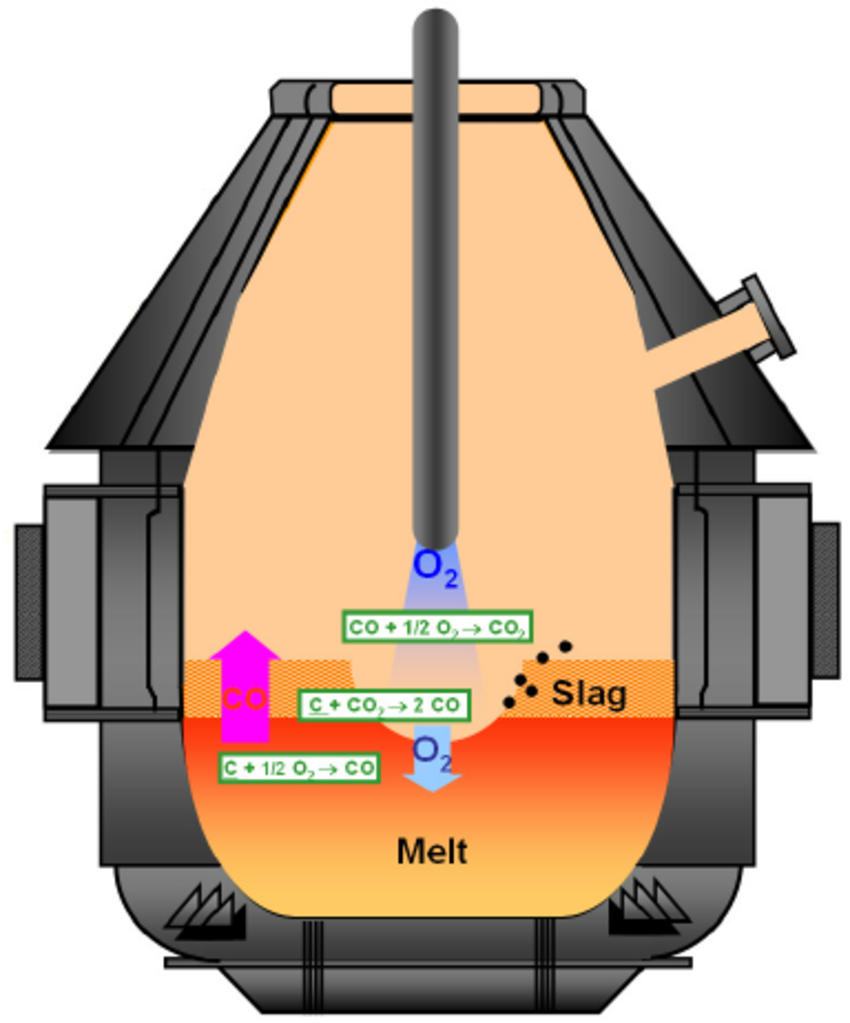
Magnesia carbon brick used in BOF
Fused magnesia: MgO>97.5%, CaO/SiO2>2, large crystals
Flake graphite: Flake graphite-197% (-100 mesh means that particles under 0.15mm account for more than 97%)
Binding agent: resinoid
Additive: alumina powder, silica powder, B4C, Al-Mg alloy
The mechanism of additives: a. additives can react with oxygen in preference to carbon; b. the products after the reaction can make the volume expand, eg, Al2O3, MA and SiO2 can fill the pores and prevent the oxidization of graphite.
High strength magnesia carbon bricks used in the impact areas have higher high temperature flexural strength, up to 16-20 MPa, by adding antioxidants such as alumina powder, but they have a high expansion coefficient (14.4X10-6·℃-1 25℃-1450℃) and poor slag resistance and are easy to spall.
The manufacturing process includes material batching, molding and heat treatment.
Magnesia cannot be too fine. 180 mesh or smaller is enough. If too fine, MgO is easy to be reduced to Mg.
Other refractory materials used in BOF
Slag splashing technology: After tapping, part of the slag is left. Slag-forming agents (magnesium ball or light-burned dolomite) are added to improve the MgO content in slags. Blow oxygen with oxygen lances to make the slag splash and hanging on the brick wall.
Impact area repair materials/large area repair materials: Fused magnesia, sintered magnesia+ Asphalt+binder (oil, diesel, etc.)
The using method of large area repair materials: After tapping, the materials are shoveled into the furnace and fill the damaged area by automatic firing and automatic flowing. Asphalt in the bottom binds with magnesia due to lack of oxygen.
Trunnion gunning material: magnesia + lime + water, high pressure air gunning, several furnace once.
Taphole repair material: magnesite + resin
Mouth magnesia ramming mass: magnesia + chrome green
EAF lining refractory materials
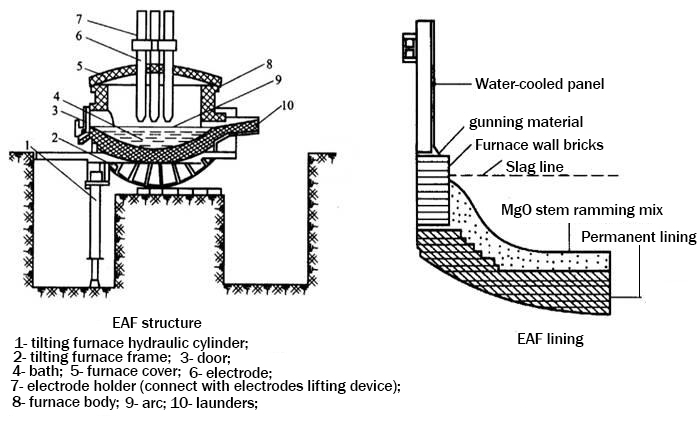
Refractory materials used in the EAF cover
Refractory materials used in the EAF wall
Technical measures to improve the service life of furnace wall refractory materials:
Large crystal magnesia: high purity, low SiO2, B2O3, high CaO/SiO2, grains greater than 150 μm
High-purity graphite: species, size distribution, purity
Additives: Al, Si, Mg, alloys, borides (ZrB2, CaB2, Mg2B3), B4C
Vacuum Oil immersed: it can close pores and improve corrosion resistance
Binding agent: phenolic resin (high carbon residue 50-60%), asphalt, asphalt - resin composite.
EAF bottom
Calcium magnesium iron ore properties: the main mineral phase include MgO, C2F, C4AF, C2S and C3S
Characteristics: have a high content of C2F, good sintering properties, good corrosion resistance to FeO and strong resistance to slag penetration.
Conductive fired MgO-C bricks and magnesia carbon ramming mass used in DC electric stoves
Refractory used EAF tapping system
EBT-Eccentric Bottom Tapping
Refractory materials used in the Taphole include high strength magnesia carbon bricks(C≥20%) and Al2O3-SiC-C bricks
Tapping hole drainage sand: a. Magnesia forsterite + + carbon black; b. Calcium magnesium iron ore
New tapping technologies include CBT (Centre bottom tapping), OBT (Offcentre Bottom Tapping), RBT (Round Bottom Tapping) and HOT (Horizontal tapping).
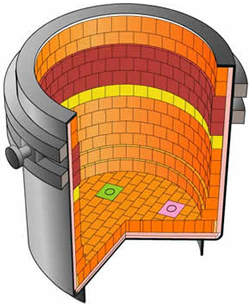
Refractory materials used in the ladle
Porous plugs: they are developed from the diffuse type to directional type and casted by corundum and chrome corundum castables, but they are difficult to synchronize with the service life of linings.
Rapid replacement of porous plugs: the bottom panel is welded on the bottom of the ladle. When installing permeable brick, porous plugs are clamped with the clamping device and in the center position. When replacing, loose the plugs.
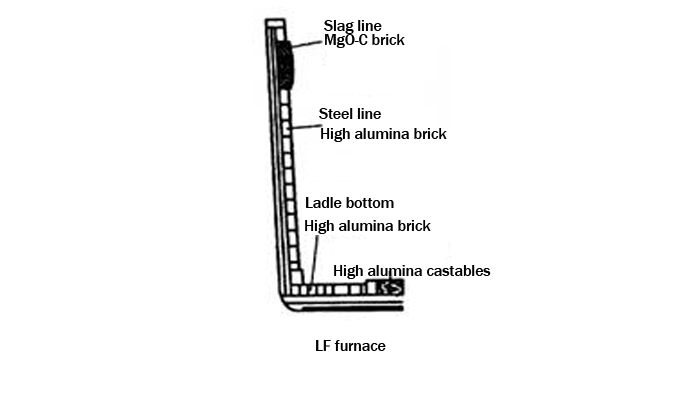
Damage reasons for LF (V) linings include:
1) Chemical reaction and corrosion
Slags react with bricks and form unstable mineralogical phases around grain boundaries: C2S, C3MS2, CMS, C2AS, etc.
2) Volatilization under high temperature and vacuum
Comparison of different evaporation rates of refractory materials: fused magnesia chromite> Magnesia> zircon> limestone> dolomite
3) Erosion by slags
Slags penetrate into the bricks through the pores resulting in an easy-to-peel metamorphic layer.
4) Thermal shock and mechanical erosion
Refractory materials used in slag lines are mainly high quality magnesia carbon bricks which contains anti-oxidant ZrB2 (1.5%).
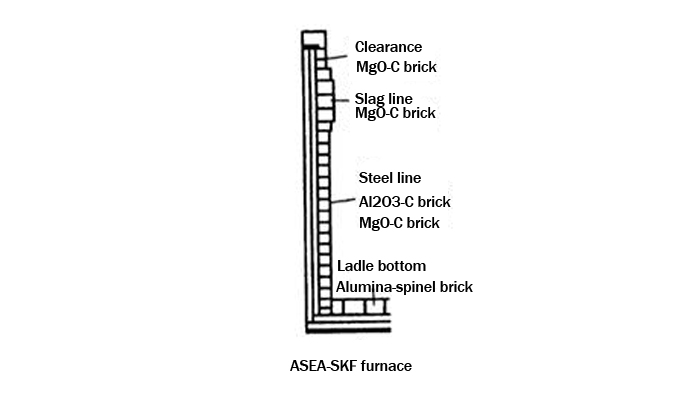
Slag line: Magnesia Carbon Bricks, magnesia chrome brick, magnesia brick, magnesia dolomite brick, high alumina brick (A1203> 85%)
75% high alumina bricks and castables are used in sidewalls and ladle bottom. Alumina carbon bricks are used in the parts in the molten steel.
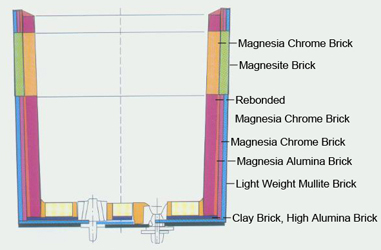
The VOD lining
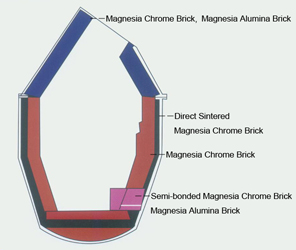
Cap: common magnesia chrome brick, alumina plastic materials
Lining: Direct bonded magnesia chrome brick, rebound magnesia chrome brick, semi-rebound magnesia chrome brick
Tuyere brick: high-purity direct bonded magnesia chrome brick, rebound magnesia chrome brick
AOD magnesia calcium brick
Cap: Bituminous Bound dolomite brick
Wall: dolomite brick
Bottom: magnesia dolomite brick
Tuyere Zone: ultra-high temperature sintering dolomite brick, fused dolomite brick
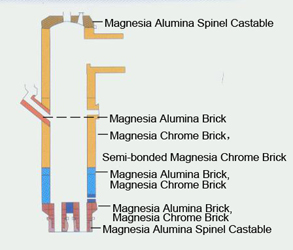
The modern steel production process generally includes material processing, iron making, steel making, rolling, energy supplying and transportation. It is a complex and huge production system.
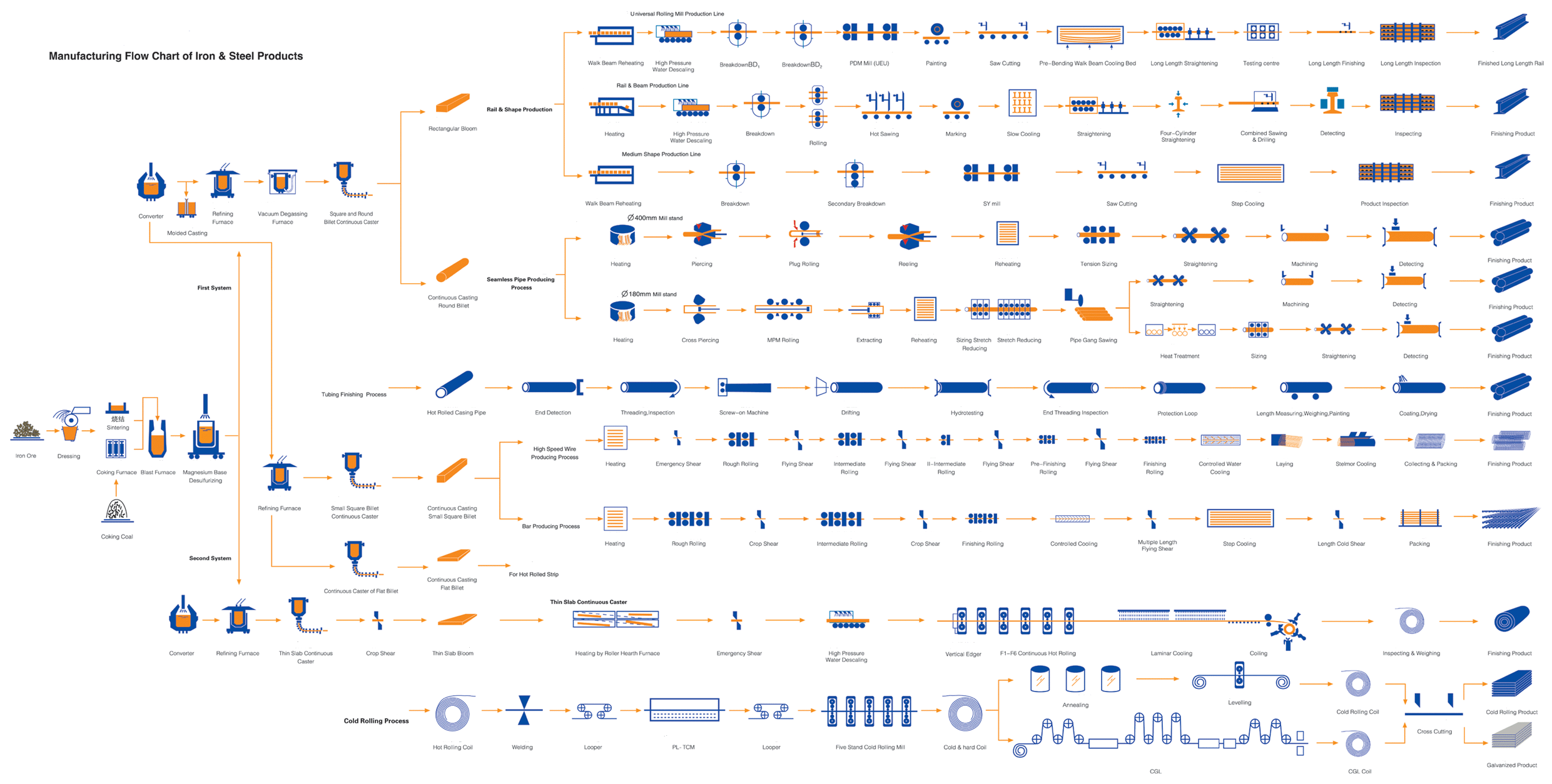
(1) Raw material smelting
Raw materials are the basis of blast Furnace Smelting. Fine materials are the basic guarantee for the stable operation of blast furnaces and high output, high quality, low cost and longevity.
The main raw materials used in the blast furnace include iron ore (natural and artificial high - grade ore), fuel (coke and blowing fuel) and flux (limestone and dolomite). Smelting one ton of pig iron takes about 1.60-1.65 tons of 63% iron ore.
(2) Iron making
Blast furnace iron making is a traditional iron making method fueled with coke. It cooperates with the BOF. It is currently the main method of steel production. The dominant position of the blast furnace for iron making is not expected to change in quite a long time. The nature of the blast furnace iron making is the reduction process of iron. Coke works as fuel and a reducing agent to reduce the iron ore or iron-containing materials from oxides or mineral status (such as Fe2O3, Fe3O4, Fe2SiO4, Fe3O4 • TiO2, etc.) into liquid pig iron.
During the smelting process, charge (ore, flux, coke) is loaded into the furnace from the top through the feeding devices according to the determined proportion. High temperature hot air blown into from the bottom generates reductive coal gas through reaction with coke and liquid slags and forms iron in the hearth by heating, reducing and melting charge. During the rising process, the temperature of the coal gas drops, the composition changes gradually and it finally forms blast furnace gas discharged from the top.
(3) Steel making
Steel and pig iron are mainly iron-based and contain iron-carbon alloy containing a small amount of carbon, silicon, manganese, phosphorus, sulfur and other elements. The difference between them is the content of carbon.
The main steps of steel making includes 1) decarbonization; 2) dephosphorization; 3) desulfurization; 4) deoxy; 5) nitrogen, hydrogen or the like; 6) non-metallic inclusion removal; 7) alloying; 8) heating 9) solidified molding.
The main process of steel making includes: (1) molten iron pretreatment; (2) BOF or EAF steelmaking; (3) refining (secondary refining); (4) continuous casting.
The steel-making process is an oxidation process. The main means of removing impurities is blowing oxygen gas into bath and adding slagging agent to form slags. The decarbonization reaction is the primary means of steel-making process. Silicon, manganese, phosphorus, sulfur and other elements are also removed by the oxidation reaction. The raw materials for steel making include pig iron, steel scrap, flux (limestone), Deoxidizer (ferrosilicon, ferromanganese, aluminum, etc.), alloys and other materials.
(4) Continuous casting
Continuous casting is a step to continuously cast molten steel into billets with a continuous casting machine. Compared to molding, continuous casting has the following advantages:
1) Simplifying the process and energy saving;
2) Reducing the cutting head rate of billets and the metal recovery rate is higher than that of molding by 7-12%;
3) Efficient solidification;
4) Optimized forming.
Continuous Casting process: molten steel is poured into crystallizers through the tundish and rapidly cooled into a solidified shell with a certain thickness, but the inside of the slab is still liquid. The lower portion of the billet connects with a dummy bar extending into the crystallizer bottom. After pouring begins, the casting machine pulls the billets out at a constant speed from the crystallizer through the dummy bar. When billets pass through a continuous casting secondary cooling zone, it is further cooled by water until it is completely solidified. Completely solidified billets are cut into a predetermined length after straightened with a straightening machine and shipped out by the conveyor roller.
(5) Rolling
The rolling process is the process to make workpiece produce plastic deformation by pulling it into the rollers with a different direction of rotation with the friction force between it and the rollers. The general rolling process can be divided into: heating, rough rolling, intermediate rolling, finishing rolling and fine finishing.
During the steel production, since work environments and requirements are different in different furnaces, refractory materials used in them are different.
(1) BOF
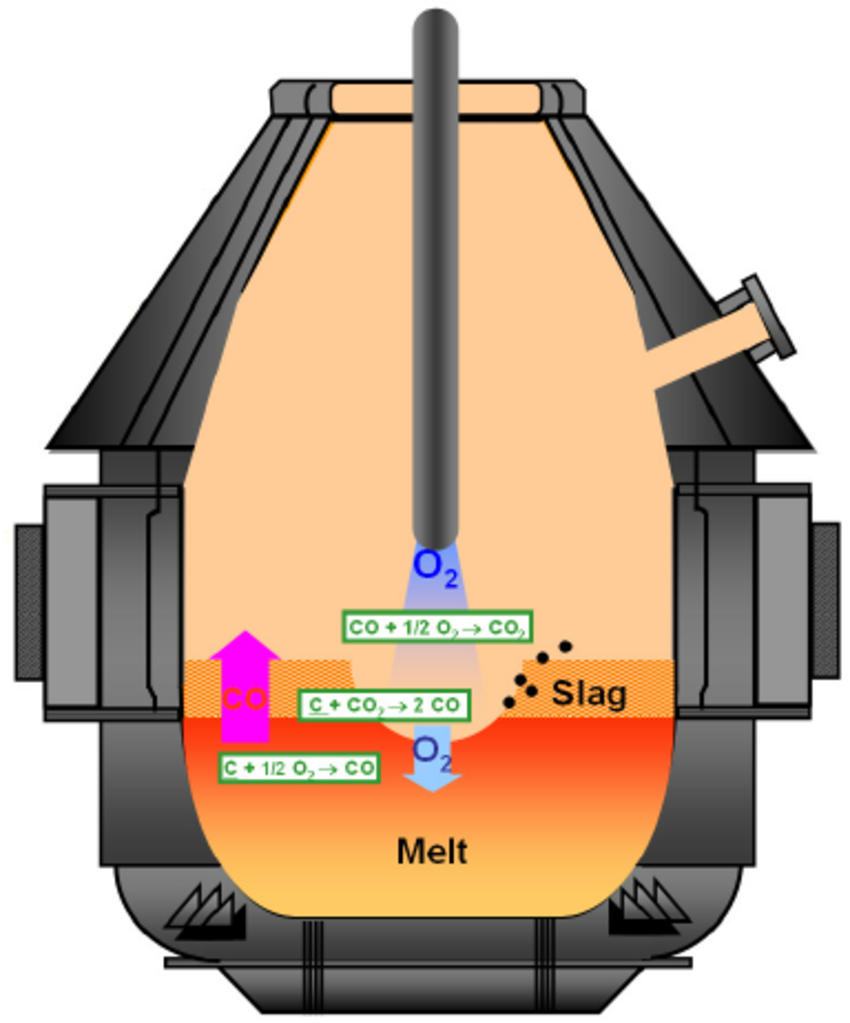
Magnesia carbon brick used in BOF
Brand | MgO, % | C, % | Bulk density, g/cm3 | Apparent porosity, % | Cold Crushing Strength, MPa | High temperature flexural strength(1400℃X30m),MPa |
MT-10 | ≥80 | ≥10 | ≥3.00 | ≤5 | ≥40 | ≥8 |
MT-12 | ≥80 | ≥12 | ≥3.00 | ≤4 | ≥40 | ≥12 |
MT-14 | ≥75 | ≥14 | ≥2.95 | ≤4 | ≥40 | ≥12 |
Flake graphite: Flake graphite-197% (-100 mesh means that particles under 0.15mm account for more than 97%)
Binding agent: resinoid
Additive: alumina powder, silica powder, B4C, Al-Mg alloy
The mechanism of additives: a. additives can react with oxygen in preference to carbon; b. the products after the reaction can make the volume expand, eg, Al2O3, MA and SiO2 can fill the pores and prevent the oxidization of graphite.
High strength magnesia carbon bricks used in the impact areas have higher high temperature flexural strength, up to 16-20 MPa, by adding antioxidants such as alumina powder, but they have a high expansion coefficient (14.4X10-6·℃-1 25℃-1450℃) and poor slag resistance and are easy to spall.
The manufacturing process includes material batching, molding and heat treatment.
Magnesia cannot be too fine. 180 mesh or smaller is enough. If too fine, MgO is easy to be reduced to Mg.
Other refractory materials used in BOF
Brand | MgO, % | CaO, % | Bulk density, g/cm3 | Apparent porosity, % | Cold Crushing Strength, MPa(110℃X24h) | Reheating linear change(1500℃X2h), % |
MZ-94 burned magnesia brick | ≥94 | ≤2 | ≥2.95 | ≤18 | ≥60 | -0.2-0 |
Large area repair materials | ≥80 | 5-10 | ≥2.20 | ≥3.0 | ||
ZLD-80D bottom ramming mass | ≥80 | ≥10 | ≥2.60 | ≥5.0 | ||
ZLC-80X Taphole repair materials | ≥80 | 2-4 | ≥2.40 | -1.0-0 | ||
MC-5H magnesia carbon mortar | ≥90 | ≥5 | ||||
MS-95 Magnesia filling material | ≥95 | ≤2 | ||||
ZLK-85/3D mouth magnesia ramming mass | ≥85 | ≥3 | ≥2.60 | ≥4.0 | -1.0-0 |
Slag splashing technology: After tapping, part of the slag is left. Slag-forming agents (magnesium ball or light-burned dolomite) are added to improve the MgO content in slags. Blow oxygen with oxygen lances to make the slag splash and hanging on the brick wall.
Impact area repair materials/large area repair materials: Fused magnesia, sintered magnesia+ Asphalt+binder (oil, diesel, etc.)
The using method of large area repair materials: After tapping, the materials are shoveled into the furnace and fill the damaged area by automatic firing and automatic flowing. Asphalt in the bottom binds with magnesia due to lack of oxygen.
Trunnion gunning material: magnesia + lime + water, high pressure air gunning, several furnace once.
Taphole repair material: magnesite + resin
Mouth magnesia ramming mass: magnesia + chrome green
(2) EAF
EAF lining refractory materials
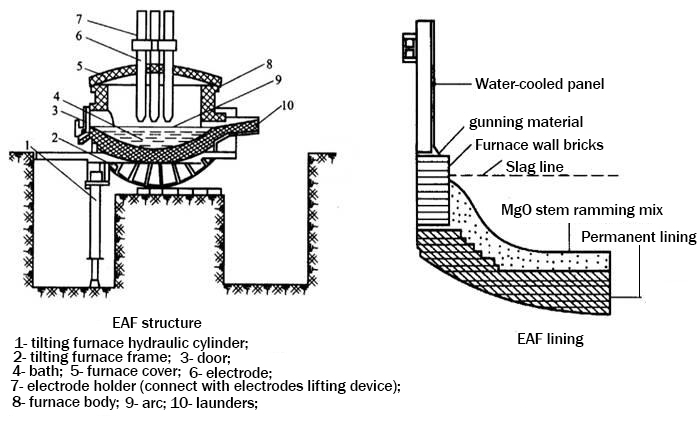
Refractory materials used in the EAF cover
Castable | Raw material | Binding agent | Auxiliary materials | Additives |
High alumina castable | Grade bauxite |
Calcium aluminate cement Al203-80 |
Corundum powder + Steel Fiber |
Trimer/hexametaphosphate |
Mullite castable | Mullite |
Calcium aluminate cement Al203-80 |
Corundum powder + Steel Fiber | Trimer/hexametaphosphate |
Corundum castable | Fused corundum/dense corundum |
Calcium aluminate cement Al203-80 |
α-Al2O3 | Organic water reducing agent |
Chrome corundum castable | Fused corundum/dense corundum |
Calcium aluminate cement Al203-80 |
α-Al2O3+ Chromium oxide powder / Chrome Corundum powder | Dimer/hexametaphosphate |
Property | Al2O3, % | Cr2O3, % | CaO, % |
CCS, MPa (110℃X24h) |
CCS, MPa (1550℃X3h) |
Corundum castable | >93 | _ | <1.2 | >60 | <100 |
Chrome corundum castable | >92 | 3-5 | <1.2 | >60 | >110 |
Refractory materials used in the EAF wall
Application Part | Materials |
Main furnace | Direct bonded magnesia chrome brick, Prereacted magnesia chrome brick, Magnesia brick |
Slag line | Oil immersed magnesia brick, direct bonded magnesia chrome brick, cast magnesia brick, MgO-C brick |
Hot spot | Oil immersed magnesia brick, direct bonded magnesia chrome brick, cast magnesia chrome brick, MgO-C brick |
Large crystal magnesia: high purity, low SiO2, B2O3, high CaO/SiO2, grains greater than 150 μm
High-purity graphite: species, size distribution, purity
Additives: Al, Si, Mg, alloys, borides (ZrB2, CaB2, Mg2B3), B4C
Vacuum Oil immersed: it can close pores and improve corrosion resistance
Binding agent: phenolic resin (high carbon residue 50-60%), asphalt, asphalt - resin composite.
EAF bottom
Application Part | Materials |
Insulation layer | A layer of asbestos, diatomite powder on asbestos, insulation bricks flat laid on them |
Permanent layer | Burned magnesia brick (MgO 95% -96%), Bituminous Bound magnesia brick, stretcher bond |
Working layer |
Knotted bottom; magnesia + asphalt, tar (or brine, sodium silicate), calcium magnesium iron ore Masonry hearth: Bituminous Bound magnesia brick, brine bonded magnesia brick |
Characteristics: have a high content of C2F, good sintering properties, good corrosion resistance to FeO and strong resistance to slag penetration.
Chemical Composition, % | Bulk density, g/cm3 | |||||
MgO | CaO | Fe2O3 | SiO2 | Al2O3 | Grain size, mm | |
≥82 | 6-7 | 7-8 | ≤1.5 | ≤1.0 |
0-8 0-5 |
≥2.40 |
Refractory used EAF tapping system
EBT-Eccentric Bottom Tapping
Refractory materials used in the Taphole include high strength magnesia carbon bricks(C≥20%) and Al2O3-SiC-C bricks
Tapping hole drainage sand: a. Magnesia forsterite + + carbon black; b. Calcium magnesium iron ore
New tapping technologies include CBT (Centre bottom tapping), OBT (Offcentre Bottom Tapping), RBT (Round Bottom Tapping) and HOT (Horizontal tapping).
(3) Ladle
Ladle is important equipment for steelmaking. Refractories used in the ladle are various and demanding.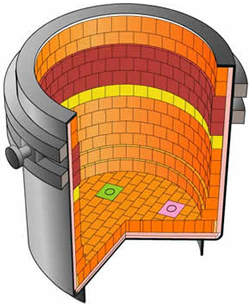
Refractory materials used in the ladle
Slag line | Ladle Wall | Ladle bottom | Ladle bottom Refractory | |
Material |
Magnesia Carbon Bricks, Alumina magnesia carbon brick |
Low-carbon Magnesia Carbon Bricks (C= 5-14%), Alumina magnesia carbon bricks, alumina magnesia non-burned brick, alumina magnesia castable | Alumina magnesia carbon bricks, alumina magnesia castable, Corundum spinel castables | Pocket block, Permeable bricks, porous pocket block, drainage sand (chrome ore - silica) |
Castables | Raw materials | Auxiliary materials | Binding agents | Additives | Applications |
High-grade | Tabular alumina + spinel | α-Al2O3 | Calcium aluminate cement -80 | Hexametaphosphate | Large ladle |
Mid-grade | Fused magnesia + spinel | _ | Calcium aluminate cement -80 | Hexametaphosphate | Medium ladle |
Low-grade | Bauxite + sintered magnesia | _ | Silica fume | Hexametaphosphate | Small ladle |
Raw materials | Auxiliary material | Binding agent | Additives | |
Magnesia Carbon Bricks | Fused magnesia, sintered magnesia | Graphite | Thermosetting phenolic resin | Alumina powder, silica powder, etc. |
Alumina magnesia carbon bricks | Fused magnesia, sintered magnesia, bauxite, brown corundum | Graphite | Thermosetting phenolic resin | |
Alumina magnesia non burned bricks | High-grade bauxite, corundum, fused magnesia | Spinel | Water glass, Cement, Brine, Waste paper pulp | Hexametaphosphate |
Rapid replacement of porous plugs: the bottom panel is welded on the bottom of the ladle. When installing permeable brick, porous plugs are clamped with the clamping device and in the center position. When replacing, loose the plugs.
(4) LF Furnace
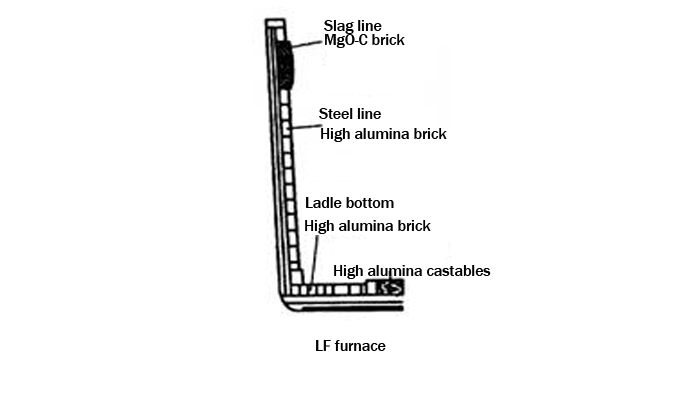
Damage reasons for LF (V) linings include:
1) Chemical reaction and corrosion
Slags react with bricks and form unstable mineralogical phases around grain boundaries: C2S, C3MS2, CMS, C2AS, etc.
2) Volatilization under high temperature and vacuum
Comparison of different evaporation rates of refractory materials: fused magnesia chromite> Magnesia> zircon> limestone> dolomite
3) Erosion by slags
Slags penetrate into the bricks through the pores resulting in an easy-to-peel metamorphic layer.
4) Thermal shock and mechanical erosion
Refractory materials used in slag lines are mainly high quality magnesia carbon bricks which contains anti-oxidant ZrB2 (1.5%).
(5) ASEA-SKF furnace
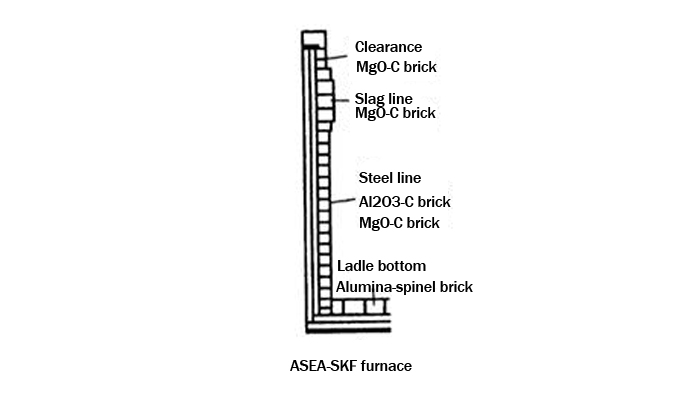
Slag line: Magnesia Carbon Bricks, magnesia chrome brick, magnesia brick, magnesia dolomite brick, high alumina brick (A1203> 85%)
75% high alumina bricks and castables are used in sidewalls and ladle bottom. Alumina carbon bricks are used in the parts in the molten steel.
(6) VOD furnace
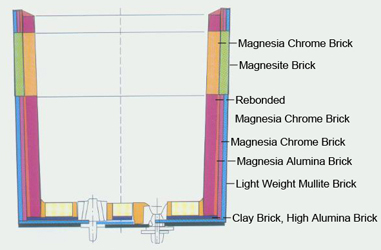
The VOD lining
Item | Direct bonded magnesia chrome brick | Rebound magnesia chrome brick | Semi-rebound magnesia chrome brick | High calcium magnesia dolomite brick | Magnesia dolomite brick |
MgO/% | 73.0 | 50.7 | 53.4 | 79.3 | 87.5 |
Cr2O3/% | 13.6 | 29.0 | 27.2 | ||
CaO/% | 0.9 | 1.1 | 0.8 | 18.9 | 10.5 |
B.D./g·cm-3 | 3.05 | 3.31 | 3.34 | 3.11 | 2.97 |
A.P./% | 16.8 | 14.4 | 14.3 | 11.4 | 14.7 |
CCS/MPa | 89.2 | 98.8 | 54.0 | 87.0 | 87.0 |
HMOR/MPa (1480℃) |
9.1 | 13.9 | 76 | 3.3 | |
Thermal shock resistance (1200℃ air cooling) / times |
6 | 10 | 10 | ||
Application area | Sidewall, ladle bottom | Slag line | Slag line, sidewall | Slag line | Slag line |
(7) AOD furnace
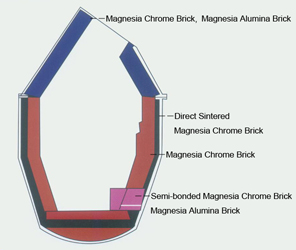
Cap: common magnesia chrome brick, alumina plastic materials
Lining: Direct bonded magnesia chrome brick, rebound magnesia chrome brick, semi-rebound magnesia chrome brick
Tuyere brick: high-purity direct bonded magnesia chrome brick, rebound magnesia chrome brick
AOD magnesia calcium brick
Cap: Bituminous Bound dolomite brick
Wall: dolomite brick
Bottom: magnesia dolomite brick
Tuyere Zone: ultra-high temperature sintering dolomite brick, fused dolomite brick
(8) RH furnace
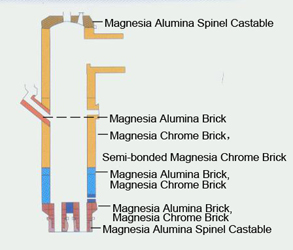
Contact Us
- E-mail :sales@sunriserefr.com
- Phone : +86-371-63838939
- Fax:+86-371-63835539
- Company Address : No.36 Fengchan Road Of Zhengzhou, Henan, China (Mainland)