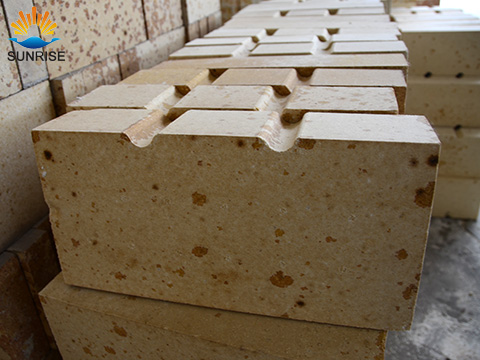
Silica brick for glass kiln
- Flux index:≤0.7
- 0.2MPa refractoriness under load:≥1660
- Apparent porosity:≤22%
- True density:≤2.35 g/cm3
Products List
- Silica brick for glass kiln...
- BG-98 superior silica bricks for gla...
- Insulating silica brick...
- High thermal shock resistance and ze...
- High bulk density and High thermal c...
- Unshaped refractory Silica Refractor...
- Silica brick for hot blast stove...
- Silica brick for coke oven...
- Silicon brick for carbon furnace...
Classic Case
-
British Refractories customers to
June 7, 2011 the British Refractories Company custo...
-
Turkish customers to visit our fa
On 26 July,2013 Turkey customers visited our fact...
Refractory Knowledge
Silica bricks for glass furnace refers to the silicon refractory product used in the high temperature part of the glass kiln (not in contact with the glass liquid), it is a kind of acid refractory mainly made from tridymite, cristobalite and a small amount of residual quartz as well as glass phase. The raw refractory material is natural silica sand whose SiO2 content should be more than 96%. The higher SiO2 content in silica sand, the higher temperature silica bricks resist.
Glass kiln silica brick has high temperature and volume stability, no pollution to glass liquid, chemical corrosion resistance, small bulk density, and can reduce the weight of furnace body.
▶ Silica Bricks for Glass Melting Furnaces Feature:
◆ The high temperature volume is stable, and the furnace body does not change due to the temperature fluctuation surface. Because the silicon brick has a high load softening temperature and a small creep rate, the glass kiln can keep the furnace body from deforming at 1600 ° C, and the structure is stable;
◆ No pollution to the glass liquid. The main component of silica brick is SiO2. If it is used, if there is any drop or surface droplet, silica bricks for glass melting furnace will not affect the quality of the glass liquid;
◆ Resistance to chemical attack. The superstructure silicon brick is eroded by R2O gas in the glass batch, and a smooth metamorphic layer is formed on the surface, which makes the erosion speed lower and protects;
◆ The bulk density is small, which can reduce the weight of the furnace body;
Silica bricks are used in the roof and superstructure of glass melting tanks as well as for hot repairs.
▶ How to Reduce the Consumption of Silica Bricks in Glass Furnaces:
Due to the high load-softening temperature, light weight and low price advantage of silica bricks,in order to increase the melting temperature and extend the overall life of the kiln, the small furnace mouth and the chest wall are changed to cast bricks, and some of the domes or parts thereof are changed to other materials. The consumption ratio of silica bricks may be reduce.
Silica brick for glass kiln |
BG-95 |
BG-96B |
BG-96A |
|
SiO2 ≥ |
95 |
96 |
96 |
|
Fe2O3 ≤ |
1.2 |
1.0 |
0.8 |
|
Flux index ≤ |
0.7 |
0.6 |
0.5 |
|
0.2MPa refractoriness under load (℃) ≥ |
1660 |
1670 |
1680 |
|
Apparent porosity (%) ≤ |
22 |
22 |
22 |
|
Cold crushing strength (MPa) |
Unit weight<20kg ≥ |
35 |
35 |
35 |
Unit weight ≥ 20kg ≥ |
30 |
30 |
30 |
|
True density (g/cm3) ≤ |
2.35 |
2.34 |
2.34 |
If you have any needs our help or are interested in our products, you can click online advisorychat with us online, or call our customer service telephone: 0086-0371-63838939. We will sincerely serve for you!