Products List
- Silica brick for glass kiln...
- BG-98 superior silica bricks for gla...
- Insulating silica brick...
- High thermal shock resistance and ze...
- High bulk density and High thermal c...
- Unshaped refractory Silica Refractor...
- Silica brick for hot blast stove...
- Silica brick for coke oven...
- Silicon brick for carbon furnace...
Classic Case
-
British Refractories customers to
June 7, 2011 the British Refractories Company custo...
-
Turkish customers to visit our fa
On 26 July,2013 Turkey customers visited our fact...
Refractory Knowledge
How to Prevent and Reduce the Erosion of Refractories in Glass Kilns
Date:2018-06-29 10:16 From:Zhengzhou Sunrise Refractory Author:admin
Glass furnace kiln powder, glass liquid and flame gas will erode the refractory material at high temperature, so that the glass kiln refractory material is dissolved, peeled, thinning, deterioration, recrystallization and other effects, known as the erosion of the refractories .
The erosion effect of the refractories of the glass kiln is manifested in the complicated phase reaction between the molten glass and the refractories. The glass melt first dissolves the free SiO2 in the refractories. The dissolution rate of mullite is relatively small, and it accumulates at the interface between the molten glass and the refractory material. Although the small crystalline mullite is dissolved, the large crystalline mullite even increases in use. After the refractories are eroded, the SiO2 and Al2O3 components are added to the melt that comes into contact with it. The melt will diffuse into the rest of the glass. During the diffusion process, the composition of the melt changes, SiO2 and alkalinity increase, and β-Al2O3, nepheline and feldspar crystallization aggregates occur in the interface, and the refractory material is also in contact with the molten glass. On the surface, the first is the mullite layer, followed by the nepheline or feldspar crystalline layer, followed by the uneroded refractories. After the refractories are dissolved, the viscosity of the glass liquid is increased, and a refractory protective layer is formed on the surface of the refractory material, which weakens the effect of continued erosion. This balance is destroyed, and the corrosion between the glass and the refractory material will occur again.
The soda ash, thenardite, borates, fluorides, and oxides in the batch material react with the surface of the refractory material at a high temperature to generate eutectic or loose material, and continue to use the alternate reaction of voids or interfaces of the refractory material itself. The internal diffusion of the brick body leads to erosion of the refractory material. The corrosion mechanism of the various salts and compounds mentioned above is different. Glauberite is much more effective than the soda ash in the erosion of refractory materials.
The erosion effect of the material powder on the material mainly manifests itself in the erosion of the refractory material by the alkaline vapour evaporating from the powder at high temperature, such as the erosion of the surface of the silica brick, the internal "rat hole", etc. Petrochemical effects. In addition, the ultra-fine powder flying in the powder aggregates in the grid of the regenerator, forms tumors, and blocks the lattice holes. In severe cases, the lattice brick is collapsed, damaged, and forced to be repaired. Corrosion increases with increasing temperature, and a 50-60°C increase in melting temperature will shorten the useful life by about one year. The front face wall, the feeding port, the front space of the melting section, the pool wall, the small furnace, and the upper lattice body of the regenerator are all subject to the erosion of the material powder.
The combustion products of coal gas and heavy oil (including corrosive gases such as SO2 and V2O5) and the volatile components of the individual batch materials also corrode the refractory materials in the flame space, small furnaces, regenerators, etc. Refractory materials in different glass kilns will react with each other and become damaged at high temperatures. For example, between 1600°C and 1650°C, clay bricks and silica bricks will react badly. High-alumina bricks and silica bricks will react moderately. The fused zirconia corundum bricks will react violently with the silica bricks, causing serious eutectic melting. The fused zirconia corundum brick reacts moderately with the quartz brick and the white basalt, and therefore a transition material should be provided between the fused zirconia corundum brick and the silica brick.
The checker bricks used in the regenerator are also damaged by the redox atmosphere. The damage mechanism is mainly due to the difference in the valence state of the variable-valent ions due to the oxidation and reduction states, different coordination states, and volume changes in the reactant phases, resulting in a decrease in strength of the brick body. And damage.
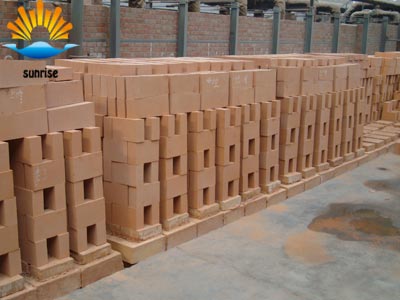
Contact Us
- E-mail :sales@sunriserefr.com
- Phone : +86-371-63838939
- Fax:+86-371-63835539
- Company Address : No.36 Fengchan Road Of Zhengzhou, Henan, China (Mainland)