Products List
- Silica brick for glass kiln...
- BG-98 superior silica bricks for gla...
- Insulating silica brick...
- High thermal shock resistance and ze...
- High bulk density and High thermal c...
- Unshaped refractory Silica Refractor...
- Silica brick for hot blast stove...
- Silica brick for coke oven...
- Silicon brick for carbon furnace...
Classic Case
-
British Refractories customers to
June 7, 2011 the British Refractories Company custo...
-
Turkish customers to visit our fa
On 26 July,2013 Turkey customers visited our fact...
Refractory Knowledge
The Selection of Particle Composition of Silica Brick
Date:2015-11-26 14:22 From:Zhengzhou Sunrise Refractory Author:admin
The density and sintering ability of silica brick depends on the nature and quantity of coarse particles and fine particles. The particle composition is very important for the density of silica brick, especially the high dense silica brick.
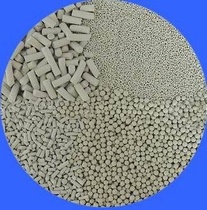
Since the raw materials are brittle, particles will be broken during the kneading and molding process. During the firing process, the phase transformation will cause the expansion and cracking of particles. Thus, the particle composition is slightly different from the particle composition of the microstructure of silica brick. In addition of packing, kneading, molding and firing will affect the production of silica brick.
Fine particles can reduce the expansion of silica brick when firing and the cracks and volume changes and improve the yield rate and the content of tridymite. If the particles are too fine, the porosity of the silica brick will be improved.
Reduce the critical particle size is one important way to reduce the cracking of silica bricks during firing. In general, the critical particle size of silica brick is 2-3mm. When the critical particle size is 2mm, there is almost no crack. If the size coefficient and the amount of mineralizing agent are reasonable, silica bricks with higher performance can be produced. When using vein quartz as the raw material, the maximum particle size is 2mm. when selecting the critical particle size, ensure the structure of bricks is stable and dense, not loose and broken. Usually for 3-1mm it is 35%-45%, 1-0.088mm 20%-25% and 0.088mm below 35%-40%.
In addition, since the fine particles in the firing process are easy to be transformed into tridymite, the fine particles are mostly added. The generally used mineralizing agents include FeO, CaO and MnO. For coke oven silica brick, 2% CaO and 2% MnO are added. For high-density high-SiO2 silica bricks, 0.8% FeO and 0.2% CaO are added. CaO and FeO are respectively added as lime and iron scale or iron filings. Industrial lignosulfonates and lime are always added as the binding agents.
The coarse particles form the skeleton. However, the phase transformation of coarse particles lasts longer and tends to occur after the phase transformation of fine particles and at the beginning of the sintering. The volume expansion of the phase transformation of coarse particles is the main reason that causes the loose structure and cracks.
In contrast with the coarse particles, fine particles are always in the pores where the coarse particles accumulate. Since the fine particles have big specific surface area, it can be melting and sintered at low temperature under the action of mineralizing agents. Fine particles less than 0.088mm are the most dynamic parts to promote sintering. Since the liquid phase can buffer stress caused by expansion and the crystalline network of tridymite can improve the strength of bricks, there should be enough fine particles in the raw materials.
During the firing process, the physical and chemical changes of coarse particles are transformation, expansion and cracking, while the physical and chemical changes of fine particles are transformation, sintering and contraction.
Contact Us
- E-mail :sales@sunriserefr.com
- Phone : +86-371-63838939
- Fax:+86-371-63835539
- Company Address : No.36 Fengchan Road Of Zhengzhou, Henan, China (Mainland)