Products List
- Silica brick for glass kiln...
- BG-98 superior silica bricks for gla...
- Insulating silica brick...
- High thermal shock resistance and ze...
- High bulk density and High thermal c...
- Unshaped refractory Silica Refractor...
- Silica brick for hot blast stove...
- Silica brick for coke oven...
- Silicon brick for carbon furnace...
Classic Case
-
British Refractories customers to
June 7, 2011 the British Refractories Company custo...
-
Turkish customers to visit our fa
On 26 July,2013 Turkey customers visited our fact...
Refractory Knowledge
The Firing Process of Silica Brick
Date:2015-12-11 09:55 From:Zhengzhou Sunrise Refractory Author:admin
Silica brick is made of quartz with addition of binders and mineralizing agents by crushing, mixing, molding, drying and firing.
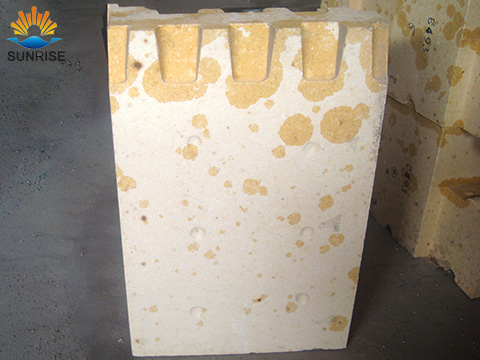
Below 600℃, since there is transformation between the α and β quartz, accompanied with volume expansion, the temperature of the center of the brick is lower than that of the surface due to the low thermal conductivity of the brick. Therefore β-α quartz transformation is not carried out at a moment, but within a certain temperature range. The transformation will not cause a lot of stress, and has little effect on the strength. Therefore, in this stage, the brick can be fired at a quick and uniform heating rate.
Above the 700℃ and within 1100-1200℃, the volume change of the brick is not big, the strength is improved gradually and no big strength is generated. The temperature can be risen quickly as long as the brick is fired evenly.
With 1100-1200℃, until the end temperature, the density of the brick is reduced greatly and the crystal transformation and volume change intensively occur in this stage. It is the key stage that determines whether the brick will crack. In this stage, the temperature should be risen slowly and uniformly.
In order to rise the temperature slowly and uniformly at the high temperature, factories always use reducing flame to fire silica bricks. It can also make the temperature in the furnace distributed evenly, reduce the temperature difference between the upper and lower furnace and avoid high temperature flame impingement.
The maximum firing temperature should not exceed 1430℃. If the temperature is too high, too much cristobalite will be generated, which will increases the scrap rate. After reaching to the maximum firing temperature, sufficient holding time should be reserved, according to the types of the furnace, the shape of the brick and the difficulty of the crystal transformation, generally 20-48 hours.
According to the heating rate, the firing process of silica brick can be divided into the following stages:
Temperature range/ ℃ | Heating rate/ (℃/h) |
20~600 | 20 |
600~1100 | 25 |
1130~1300 | 10 |
1300~1350 | 5 |
1350~1430 | 2 |
After the firing is finished, the brick should be cooled. At high temperature(600-800℃), the brick can be cooled quickly. At low temperature, since the rapid transformation of the cristobalite and tridymite will cause volume shrinkage, the brick should be cooled slowly.
When developing the firing curve, beside the above requirements, the following factors should be taken into consideration too, such as the properties of the raw materials, the amount and properties of the additives, the shape and size of the brick and the structure, size , loading method and temperature distribution of the furnace.
Contact Us
- E-mail :sales@sunriserefr.com
- Phone : +86-371-63838939
- Fax:+86-371-63835539
- Company Address : No.36 Fengchan Road Of Zhengzhou, Henan, China (Mainland)